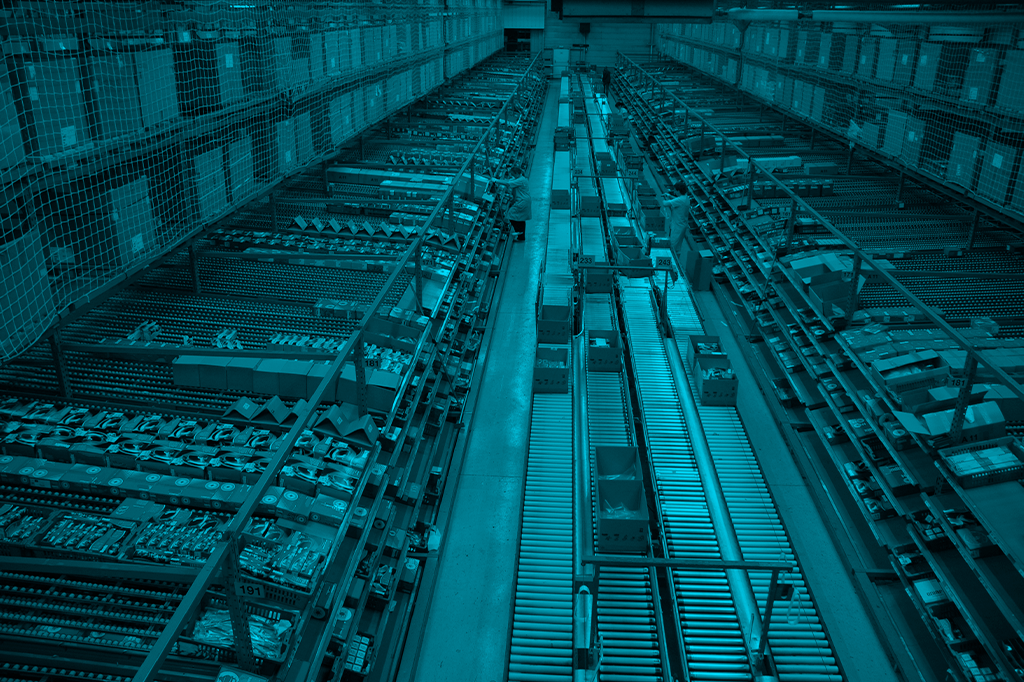
You are certainly reading this article because you want to analyze automation alternatives in materials handling for your daily life, it may even be that you are already evaluating specific solutions, however, there is always a minimum percentage of doubt due to the investment that it entails.
Don´t leave! Stay with us to analyze the key principles of materials handling, with a special focus on Automation.
What relevance does the principle of “automation” have in materials handling?
The Material Handling Institute developed 10 key principles in materials handling. We are going to talk about them below and we will talk in more depth about number eight, which corresponds to Automation.
1.- Planning. Starting from a plan that covers all the objectives, limitations and execution strategy
according to materials management is a vital point to direct any project to success.
During this stage, materials management involves all areas such as suppliers, engineers, specialists, and finances, in order to have a better focus and standardization.
2.- Standardization. Materials handling methods, equipment, controls, and software must be
standardized within limits that achieve overall performance objectives, without sacrificing flexibility, modularity and production.
3.- Work. Materials handling work should be minimized without depriving the operation of its productivity or required level of service. At this point the process cycle is key, to take care of the safety and protection of the product.
4.- Ergonomics. The design, adaptation of equipment and handling of materials is essential to ensure the safety and effectiveness of both the mental and physical tasks of the personnel.
5.- Unit load. The objective of unit loads is to transport the greatest number of products in a single
movement, either for storage or transfer for shipment. The unit load unit can be a pallet, or container, sized and configured according to each process within the supply chain.
6.- Use of space. Effective and efficient use must be made of all available space. We must remember that an incorrect layout can block the aisles and affect the operation.
7.- System. Material movement and storage activities must be integrated to form an operating system that encompasses receipt, inspection, storage, production, assembly, unification, packaging, order selection, shipping, transportation, and claims handling.
8.- Automation. Materials handling operations should be mechanized and/or automated where possible, to improve operational efficiency, increase responsiveness and improve consistency. We will delve into this principle later.
9.- Environmental impact. Environmental impact and energy consumption are criteria that must be
considered when designing and selecting material handling systems equipment. In order to reuse and not waste resources.
10.- Life cycle cost. A thorough economic analysis must be considered throughout the life cycle of the materials handling equipment. This allows you to have a clearer picture, predict and make decisions for any new method.
Why betting on automation can scale the operation?
The principle of Automation is very powerful, it represents a link that, if not chosen, could even lead to the bankruptcy of the company. Automation has become an aspect of vital importance in every industry as it ensures optimal operations that allow the required rate to be met, avoiding delays in the delivery of the finished product. The automation of materials handling allows a balance between 3 fundamental elements: operators, technology and operation.
Obviously, according to the needs of each operation, various technologies must be chosen that allow Automation, however, those that we can highlight today for their high functionality, we have the following:
- Conveyor Systems. When we must move or accumulate products, an essential ally is Conveyor Systems.
Just imagine this scenario that is still latent in more companies than you could imagine: dozens of operators moving the product, generating bottlenecks, ergonomic problems, thousands of hours invested in it and hundreds of errors due to lack of precision.
With Conveyor Systems, the productivity of transfer, accumulation, assembly, distribution, lifting, among others, increases.
- AGV´s. When the product has complex characteristics, it is chosen to integrate AGVs (automatically guided vehicles), which handle heavy loads in repetitive trajectories.
These vehicles provide multiple benefits to operators, but the two most important are: 1) repetitive transfers of human personnel are avoided and, 2) their safety is maintained by preventing them from loading heavy products.
- AS/RS systems. AS/RS equipment allows high control and guarantee of compliance with “first in and first out” of the warehouse. Integrating technologies from this range solves space problems, since it allows you to optimize the area, without losing the productivity of your operation.
Automation offers real solutions to companies that tirelessly seek continuous improvement, offering real advantages in both operation and business growth.
Are you looking for tangible, high-performance solutions? Talk to our commercial team, who will listen to your needs and design effective solutions for your organization.